Loadbearing Masonry construction can actually be faster than other systems
When used in a manner that is well suited to loadbearing masonry, and built by an experienced contractor who can keep up with timelines, you may be surprised how quickly your building takes shape
Masonry supporting the structure means coordination of trades
In a typical structure, there are many trades all working at the same time to make sure the building goes up. The more trades involved, the more likely that miscommunications or delays could occur. In a loadbearing masonry structure there are only two trades involves, the masonry contractor and the team tasked with installing the precast flooring system. The masonry contractor and the precast team can work side-by-side or even take shifts on the jobsite. Loadbearing masonry building have repeating floor plans so the timelines per storey are very consistent and easy to schedule around.
The right layouts allow for masonry to coordinate well with slab placement
Some buildings are better suited for loadbearing masonry than others. Buildings with repeating floor plans that allow for continuous masonry walls from the foundations all the way up to the top storey are crucial. When using a precast floor decking like hollowcore there are additional factors to consider like which way the planks will span. Coordination between the masonry contractor and the team installing the precast planks can speed up construction as well. Some projects have metaphorically split the building in half, one half is the masonry contractor building the walls, the other half is the precast installer installing hollowcore plank. Once each team is finished they switch sides and continue until the building is completed
After the units are laid, walls can be approved by engineer for supporting slabs relatively quickly
“This is an engineering decision and depends on several highly technical factors. That being said, Concrete Masonry Units (CMU) arrive on site at full strength and mortar strength develops very quickly, especially in compression. Without the cladding system attached to the building, the walls are subjected to mostly just the weight of the precast planks. There have been multiple studies and research project looking at the early strength of masonry that can be used to get an idea of how soon a mortar joint can support the weight of slabs, acting in compression. You would be surprised how early masonry has the capacity to support a hollow-core slab resting upon it!
If you are looking for more information, please contact CMDC for more information.
Demonstrating improved timelines
Quantifying and comparing the accelerated timeline of loadbearing masonry construction through a 3rd party
A 4-storey multi-residential building was designed using local third-party designers (Spitfire Design Co. and Valron Engineering), and the associated cost estimates and timelines were built by a local general contractor (Acadian Construction). This data was brought together by CMDC and a report was written.
The report took a model building located in Moncton, NB and it was designed using three different building materials for the main loadbearing system: wood frame (combustible construction), cast-in-place concrete and concrete block masonry. The length of the construction schedule (for structure and enclosure only) for each material is shown in Figure 1. Construction schedules are available in the study report.
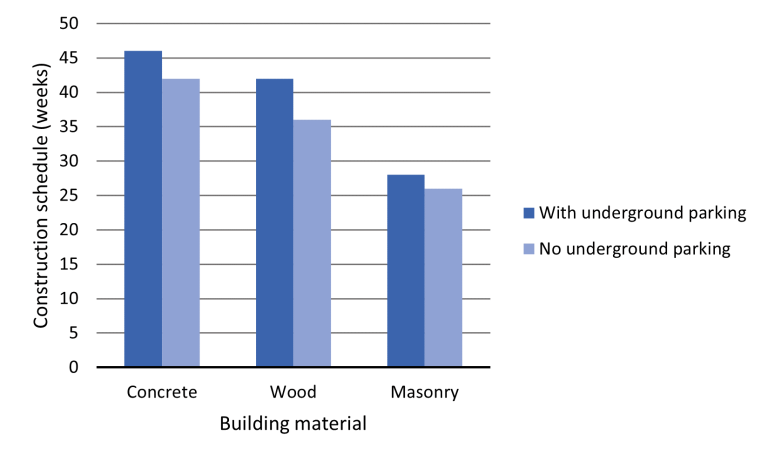
Figure 1: Construction schedule (structure and enclosure)
For the model building, the construction period of the masonry structure is shorter by 2 to 4 months compared to the construction period for the wood or cast-in-place concrete structure. The speed of masonry construction is partly due to the fact that the hollowcore slabs that form the floors do not need any shoring. This allows the installation of the enclosure elements in the lower floors to take place while the construction of the upper floor structure continues. Masonry construction also makes it possible to limit the number of different trades that need to access the site at the same time. During the installation of walls and floors, only masons are on site, and therefore the risk of confusion and conflicts on site during the erection of the structure is reduced.
The accelerated construction schedule of the masonry structure allows the client to rent the units of the building and profit from them more quickly. In addition, completing the building quicker we reduce the amount of builders risk insurance payments required. Delays due to the slower construction of the wood framed or concrete structure would therefore cause a loss of income and additional cash going out the door. With the housing crisis we are currently experiencing in Canada, there are certainly other advantages to the accelerated construction schedule of concrete block masonry structures. Rapid construction of affordable masonry housing could contribute to a solution to the housing crisis. Strong demand for housing has also pushed up rent prices and reduced vacancy rates since the report was released in 2020, increasing the value of time lost during construction.
Skeptical? Check our math
Full Study including design drawings, scheduling, budget, and even structural drawings is available as part of the full cost study
Get in touch with our team
The Canada Masonry Design Centre helps members of the design community across the country by connecting them to the resources and supports they need. Contact us today and get the conversation started!
Contact Us