Loadbearing Masonry construction is often less expensive than other systems
When you combine loadbearing masonry with a precast flooring system, add in a well planned out timeline, it is one of the most cost effective building material options out there
Save on Construction Costs
Concrete block masonry is a strong and durable system for the construction of mid-rise buildings. With all the advantages offered by this type of construction (durability, fire resistance, sound attenuation, etc.), some might expect that construction costs would be much higher than for conventional wood frame (combustible) construction. This may be the case in some parts of the world, however in many urban centres in Canada and the U.S., the cost of building a mid-rise masonry residential building is very close to (and sometimes lower than) the cost of of wood construction. CMDC’s 2019 Construction Cost Study explains how the cost of masonry construction compares to cast in place concrete and wood construction in Atlantic Canada.
The main objective of CMDC’s construction cost study was to develop a model to compare relative costs for a mid-rise multi-residential building. To do this, construction costs for three different materials and two building layouts (with and without underground parking) were estimated. The units of the model building are of a common size and layout for contemporary construction in Atlantic Canada for apartments, condominiums, and student residences, consisting of 800 ft2 one-bedroom units and 1000 ft2 two-bedroom units. Only the construction costs of the load-bearing structure and enclosure are included in this study since the details of the exterior façade, interior finish, and HVAC system may vary but are not necessary for the construction cost comparison.
The architectural plans for the model structure were developed by Spitfire Design Co. from the plan for a four-storey wood-frame building. The plan of the building, especially the layout of the walls, was therefore favourable to wood construction. The preliminary engineering design of the structure (for masonry, wood, and cast in place concrete), according to the building code in Moncton, NB, was completed by Valron Engineers Inc. Construction costs and work schedules were estimated by Acadian Construction. The construction cost analysis was carried out by CMDC, based on the information produced by the above third parties.
For the archetypal building, the cost of construction for the load-bearing structure and enclosure made of wood, masonry, and cast in place concrete is available in Table 1. This comparison shows that the price of wood construction is the least, followed by load-bearing masonry construction, and cast in place concrete construction is the most expensive.
Table 1: Construction costs of the structure and enclosure
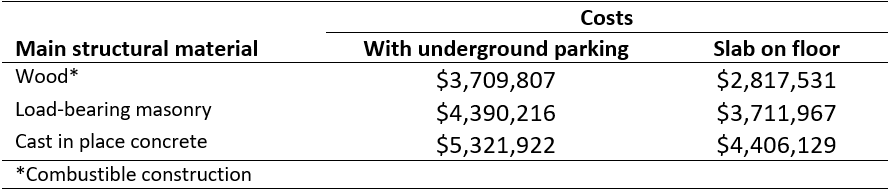
The difference between construction costs, presented in Table 1, may seem significant, however, considering that the cost of the building structure and enclosure is only about 40% of the total cost of construction, this difference begins to disappear. In addition, it would be highly likely that the costs of finishing the masonry structure could be lower than those of the wood structure, and that less material will need to be added to the base structure in order to meet the requirements of the building code in terms of sound transmission and fire resistance.
Another study was developed in 2017 in the U.S. by Walter Schneider III (Ph.D., P.E., CBO, MCP, CFO) for the National Concrete Masonry Association (NCMA) [link to: https://ccmpa.ca/resources-publications/cost-analysis-studies/]. This study was adapted for Canada with funding from the Canadian Concrete Masonry Producers Association (CCMPA). Although the study followed a different methodology than the CMDC, the conclusions are still similar. Several major cities in Canada and the U.S. were the subject of the construction cost analysis, and the analysis considered a variety of construction materials, including masonry. According to Dr. Schneider’s analysis, the construction costs for a multi-residential building in Atlantic Canada (Halifax, NS) in masonry represent an additional cost of 5% compared to wood construction (very similar to the findings of CMDC’s analysis for Moncton, NB).
The differences in methodology between Dr. Schneider’s report and the CMDC report make their conclusions all the more compelling. Dr. Schneider’s study was carried out with the same structural plan (four-storey building, about 9000 m2 total) in 25 different cities. This building layout was probably not optimal in all the targeted cities, but still gave similar results from one city to another. For the CMDC study, a four-storey model building (approximately 5300 m2 total) with larger dwellings (i.e., a larger floor area per unit) than would be expected in larger cities was selected to better represent the Moncton market. In addition, mechanical elements (HVAC), interior finishing and exterior finishing costs were included in Dr. Schneider’s analysis, but simplified (fixed price assumption for these elements, regardless of structure) for the CMDC report.
To complement the original 2017 study, Dr. Schneider also produced brief analysis reports for some of the cities included in the original report to determine the effect of construction insurance costs (builder’s risk insurance). According to these analyses, the cost of constructing a three-storey load-bearing masonry building at the end of construction represents a savings of 4 to 6% compared to lumber construction for the cities of Toronto, Boston, and Pittsburgh. In addition, fluctuating material prices mean that the price of masonry construction itself is sometimes lower than that of wood construction. For example, according to Dr. Schneider, masonry construction in Toronto in 2017 represented an additional cost of 4% compared to lumber construction, but in 2021 masonry construction represented a savings of 5% even before counting the saving in insurance costs.
In summary, two independent studies reached similar conclusions. Both studies compared load-bearing masonry construction costs with other building materials, including cast-in-place concrete and wood frame (combustible) construction. Although the analytical methods for these studies were different, their results were much the same: for a four-storey multi-residential building, load-bearing masonry construction is not much more expensive (and sometimes less) than lumber construction and offers significant savings compared to cast-in-place concrete construction.
The speed of construction in load-bearing masonry and the advantages in terms of the organization of the work (fewer trades involved at the same time on the jobsite, stable cost of materials) make this type of construction even more desirable. Once constructed, load-bearing masonry buildings are very durable and resistant to both the effects of water damage and fire. The comfort of the inhabitants is also ensured by the excellent performance of the loadbearing system to reduce the transmission of airborne noise and thanks to the thermal mass of the masonry which helps to reduce ambient temperature fluctuations. The thermal mass of masonry can also contribute to a reduction in the cost of HVAC equipment (lower peak output demands) as well as heating and cooling costs. When all these characteristics are taken into account, it becomes clear that load-bearing masonry is the ideal material for mid-rise multi-residential buildings.
Skeptical? Check our math
Full Study including design drawings, scheduling, budget, and even structural drawings is available as part of the full cost study
Get in touch with our team
The Canada Masonry Design Centre helps members of the design community across the country by connecting them to the resources and supports they need. Contact us today and get the conversation started!
Contact Us